orange_hand
..
Hi,
ich habe mir überlegt einfach einmal einen kleinen Project Thread zum Thema Midibox SEQV4 zu eröffnen. Da ich das Projekt sehr spannend finde, denke ich mir das auch andere daran gefallen finden könnten und sich vielleicht auch zu einem Midibox Projekt motivieren lassen.
Ich werde somit in unregelmäßigen Abständen etwas zum Bau des Sequenzers schreiben und auch ein paar Bilder einstellen, damit man sich das Ganze etwas besser vorstellen kann. Fangen wir erstmal an mit den Credit's. Mein besonderer Dank geht hier an:
- Thorsten Klose (aka TK)
- Jason Williams (aka Wilba)
- Tim Ellis (aka SmashTV)
Diese Experten haben im wesentlichen das Midibox Projekt auf die Beine gestellt und sind somit die Macher des Sequenzers. Ich bin immer wieder erstaunt wie gut die Ideen sind und wie professionell diese umgesetzt werden. Wer mehr über die Projekte wissen möchte der guckt auf http://www.ucapps.de und http://www.midibox.org !
Als ersten Motivator möchte ich mal die Feature Liste anführen, daran kann man schon erkennen das es sich um ein Hammerprojekt handelt (Quelle: Thorsten Klose auf http://www.ucapps.de). Ich spare mir hier mal die Übersetzung, denn wir verstehen ja sowieso alle Englisch
. Ich mache meine Dokumentationen auch zum großen Teil direkt in Englisch, da ich sie auch im Midibox Forum, sowie Wiki veröffentliche.
- optimized for live playing and editing
- intuitive user interface with flat menu hierarchy, wide screen display (2 * 2x40 = 160 characters) and 16+1 rotary encoders with menu page dependent "soft function".
- multiple MIDI Out ports (up to 11) for reduced MIDI latency
- 3 MIDI In ports (e.g. for separated MIDI clock and MIDI keyboard inputs)
- USB interface which supports USB MIDI protocol to send events more than 100 times faster
- optional Ethernet interface for sending/receiving OSC packets (or MIDI events embedded into OSC packets)
- every parameter can be modified in realtime w/o affecting the sequencer timings
- one sequencer pattern consists of 4 independent tracks
- four patterns can be played at the same time -> makes 16 tracks
- each track consists of up to 16 layers which can be assigned to various parameters (e.g. Note/Velcity/Gatelength/Chords/CC/PitchBender/Delay/Probability/Roll)
- Transpose and Arpeggiator function
- Force-to-Scale function with 166 predefined scales
- Track directions: Forward/Backward/PingPong/Pendulum/Random Dir/Random Step
- Track direction progressive parameters (Step Forward, Jump Back, Repeat, Interval, Skip, Repeat)
- free adjustable clock divider for each track. Supported timebases 1..256, normal and tripled
- available length for every track: 1-256 steps
- with 384ppqn resolution, 256th notes can be played
- loop point within track
- step events can be triggered multiple times (up to 4 times per step) with a delay value of 1-31 to realize drumrolls, ratterbeats, flams...
- 8 trigger layers for Gate/Skip/Accent/Glide/Roll/Random Gate/Random Value/No Fx
- various Groove styles (shuffle/inverted shuffle/...) + customizable Groove Templates (Delay/Length/Velocity)
- Humanizer function (random modification of note/velocity/gatelength)
- Pattern Morphing, controllable in 128 steps with a Modulation Wheel
- Echo Fx with Repeat/Delay/Feedback/Note increment/Gatelength/Delay parameters
- LFO Fx with different waveforms, synchronized period length, adjustable reset point, phase, OneShot mode. Assignable to Note/Velocity/Length/CC
- Note Limiter Fx
- Manual step triggering
- Step and Realtime Record function
- Copy/Paste/Clear function
- Scroll and Step Move function
- Random and Euclidean pattern generator
- Undo function
- parameters of multiple steps can be changed relatively and absolutely with a single rotary encoder
- parameters of multiple tracks can be changed the same time with a single rotary encoder
- Tracks and parameter layers can be muted
- Accent/Slide/CC sequences
- inbuilt MIDI mixer/controller with 128 free definable mixer maps
- inbuilt MIDI router
- virtual "Loopback port" for Master/Slave tracks
- split function for Transposer/Arpeggiator
- 8 optional CV outputs and gates for analog gear
- CV outputs can also be accessed from MIDI In (-> replaces a CV interface)
- 64 optional 1 mS drum trigger outputs
- 8*128 patterns are stored on SD Card
- 128 mixer maps are stored on SD Card
- pattern sets can be looped and chained in song mode
- phrase mode which allows to switch between the 16 predefined pattern sets (for fills/breaks/chorus, etc...)
- pattern switching can be synchronized to the measure
- MIDI Remote functions
- 2.5-300 BPM (MIDI clock master)
- external sync (MIDI clock slave)
- DIN sync output for controlling vintage sequencers
- works with 16x MIDI clock resolution (384 ppqn)
- several hardware options (e.g. a 64 Button/Duo-LED matrix)
- details and demo samples in the User Manual
- DIY ONLY!!! (commercial release neither planned, nor allowed!)
Das ist doch der Hammer, oder .... !!
So, dann fangen wir mal an mit der Basis, das Werkzeug. Ich füge einfach mal ein paar Bilder meiner Werkzeugkiste bei und beschreibe mal kurz ein paar Highlights dazu:
Zum Abisolieren von Kabeln verwende ich ausschließlich folgende Spezialzange, die ich auch immer gerne weiter empfehle. Diese Zange ist nicht billig, aber ich denke sie ist ihr Geld Wert und bringt auch einen gewissen Spaßfaktor beim Arbeiten. Diese Zange entfernt die Isolierung ohne das der Draht dabei beschädigt wird. Man muß nur einmal die Länge einstellen, die man abisolieren möchte und los gehts. Die Zange stellt sich automatisch auf die Kabeldicke und Ummantelungsdicke ein, einfach super.
Dann habe ich mir auch eine Spezialzange zum Crimpen von Steckverbindern beschafft, die ist billig und Gold Wert:
Für Bohrungen und ander mechanische Arbeiten habe ich mir einen Proxxon FBS 240/E gekauft, der ist handlich und leistet sehr gute Dienste:
Wenn man mit so einem Tool arbeitet, dann muß man auch eine Brille aufsetzen ! Health & Safety !!
Zum Löten verwende ich den Ersa Tip 260 mit bleistift-förmiger Spitze. Damit konnte ich bisher alle Projekt bearbeiten:
Dazu einen passenden Ständer:
Die Platinen spanne ich meistens in folgenden Platinenhalter ein. Der ist auch Gold Wert.
Kleinere Platinen lasse ich mit folgendem Teil halten:
Folgende Zange halte ich für absolut empfehlenswert, denn damit lassen sich auch sehr kleine Bauteile auf der Platine noch gut abschneiden:
Als nächstes kommt eine Übersicht der Komponenten des Sequenzers. Mann kann ihn ja in unterschiedlichen Ausführungen aufbauen:
Die wesentlichen Bestandteile meines MBSEQV4 sind also:
- Das Alu Gehäuse von der Firma Heidenreich
- Die Core32 Platine, die die Steuerung und Programmlogik des Sequenzers realisiert. Auf der Platine befindet sich auch der USB Port
- Die Quad IIC Platine, die nochmal 4 MIDI Out Ports, einen DinSync und einen BLM (Button Led Matrix) Port zur Verfügung stellt
- Das Ethernet Modul, welches für das OSC (open sound control) Protokoll benötigt wird. Yes, der Sequenzer hängt mit im Netz !! Hehe, wer kann schon einen Ping auf sein Gear machen
...
- Das SD Karten Modul zum Lesen und Schreiben der Projektdaten und der Konfigurationsdateien
- Die Bedieneroberfläche mit 16 Encodern und einen Haufen Tastern
- Das Front Panel, welches bei der Firma Schaeffer AG produziert werden kann
- Zwei Displays mit je 2x40 Zeichen
- Steckernetzgerät DC 9V / 2A
Wie man in meiner Kalkulation sieht, ist das Projekt nicht billig, da kommt eine Menge zusammen.
ich habe mir überlegt einfach einmal einen kleinen Project Thread zum Thema Midibox SEQV4 zu eröffnen. Da ich das Projekt sehr spannend finde, denke ich mir das auch andere daran gefallen finden könnten und sich vielleicht auch zu einem Midibox Projekt motivieren lassen.
Ich werde somit in unregelmäßigen Abständen etwas zum Bau des Sequenzers schreiben und auch ein paar Bilder einstellen, damit man sich das Ganze etwas besser vorstellen kann. Fangen wir erstmal an mit den Credit's. Mein besonderer Dank geht hier an:
- Thorsten Klose (aka TK)
- Jason Williams (aka Wilba)
- Tim Ellis (aka SmashTV)
Diese Experten haben im wesentlichen das Midibox Projekt auf die Beine gestellt und sind somit die Macher des Sequenzers. Ich bin immer wieder erstaunt wie gut die Ideen sind und wie professionell diese umgesetzt werden. Wer mehr über die Projekte wissen möchte der guckt auf http://www.ucapps.de und http://www.midibox.org !
Als ersten Motivator möchte ich mal die Feature Liste anführen, daran kann man schon erkennen das es sich um ein Hammerprojekt handelt (Quelle: Thorsten Klose auf http://www.ucapps.de). Ich spare mir hier mal die Übersetzung, denn wir verstehen ja sowieso alle Englisch

- optimized for live playing and editing
- intuitive user interface with flat menu hierarchy, wide screen display (2 * 2x40 = 160 characters) and 16+1 rotary encoders with menu page dependent "soft function".
- multiple MIDI Out ports (up to 11) for reduced MIDI latency
- 3 MIDI In ports (e.g. for separated MIDI clock and MIDI keyboard inputs)
- USB interface which supports USB MIDI protocol to send events more than 100 times faster
- optional Ethernet interface for sending/receiving OSC packets (or MIDI events embedded into OSC packets)
- every parameter can be modified in realtime w/o affecting the sequencer timings
- one sequencer pattern consists of 4 independent tracks
- four patterns can be played at the same time -> makes 16 tracks
- each track consists of up to 16 layers which can be assigned to various parameters (e.g. Note/Velcity/Gatelength/Chords/CC/PitchBender/Delay/Probability/Roll)
- Transpose and Arpeggiator function
- Force-to-Scale function with 166 predefined scales
- Track directions: Forward/Backward/PingPong/Pendulum/Random Dir/Random Step
- Track direction progressive parameters (Step Forward, Jump Back, Repeat, Interval, Skip, Repeat)
- free adjustable clock divider for each track. Supported timebases 1..256, normal and tripled
- available length for every track: 1-256 steps
- with 384ppqn resolution, 256th notes can be played
- loop point within track
- step events can be triggered multiple times (up to 4 times per step) with a delay value of 1-31 to realize drumrolls, ratterbeats, flams...
- 8 trigger layers for Gate/Skip/Accent/Glide/Roll/Random Gate/Random Value/No Fx
- various Groove styles (shuffle/inverted shuffle/...) + customizable Groove Templates (Delay/Length/Velocity)
- Humanizer function (random modification of note/velocity/gatelength)
- Pattern Morphing, controllable in 128 steps with a Modulation Wheel
- Echo Fx with Repeat/Delay/Feedback/Note increment/Gatelength/Delay parameters
- LFO Fx with different waveforms, synchronized period length, adjustable reset point, phase, OneShot mode. Assignable to Note/Velocity/Length/CC
- Note Limiter Fx
- Manual step triggering
- Step and Realtime Record function
- Copy/Paste/Clear function
- Scroll and Step Move function
- Random and Euclidean pattern generator
- Undo function
- parameters of multiple steps can be changed relatively and absolutely with a single rotary encoder
- parameters of multiple tracks can be changed the same time with a single rotary encoder
- Tracks and parameter layers can be muted
- Accent/Slide/CC sequences
- inbuilt MIDI mixer/controller with 128 free definable mixer maps
- inbuilt MIDI router
- virtual "Loopback port" for Master/Slave tracks
- split function for Transposer/Arpeggiator
- 8 optional CV outputs and gates for analog gear
- CV outputs can also be accessed from MIDI In (-> replaces a CV interface)
- 64 optional 1 mS drum trigger outputs
- 8*128 patterns are stored on SD Card
- 128 mixer maps are stored on SD Card
- pattern sets can be looped and chained in song mode
- phrase mode which allows to switch between the 16 predefined pattern sets (for fills/breaks/chorus, etc...)
- pattern switching can be synchronized to the measure
- MIDI Remote functions
- 2.5-300 BPM (MIDI clock master)
- external sync (MIDI clock slave)
- DIN sync output for controlling vintage sequencers
- works with 16x MIDI clock resolution (384 ppqn)
- several hardware options (e.g. a 64 Button/Duo-LED matrix)
- details and demo samples in the User Manual
- DIY ONLY!!! (commercial release neither planned, nor allowed!)
Das ist doch der Hammer, oder .... !!
So, dann fangen wir mal an mit der Basis, das Werkzeug. Ich füge einfach mal ein paar Bilder meiner Werkzeugkiste bei und beschreibe mal kurz ein paar Highlights dazu:
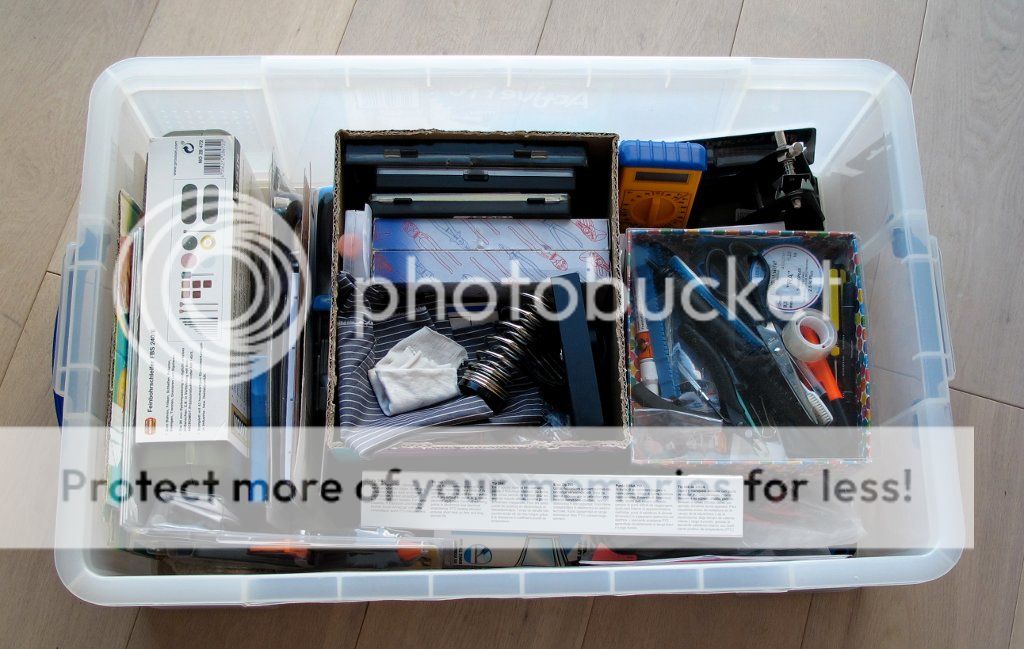
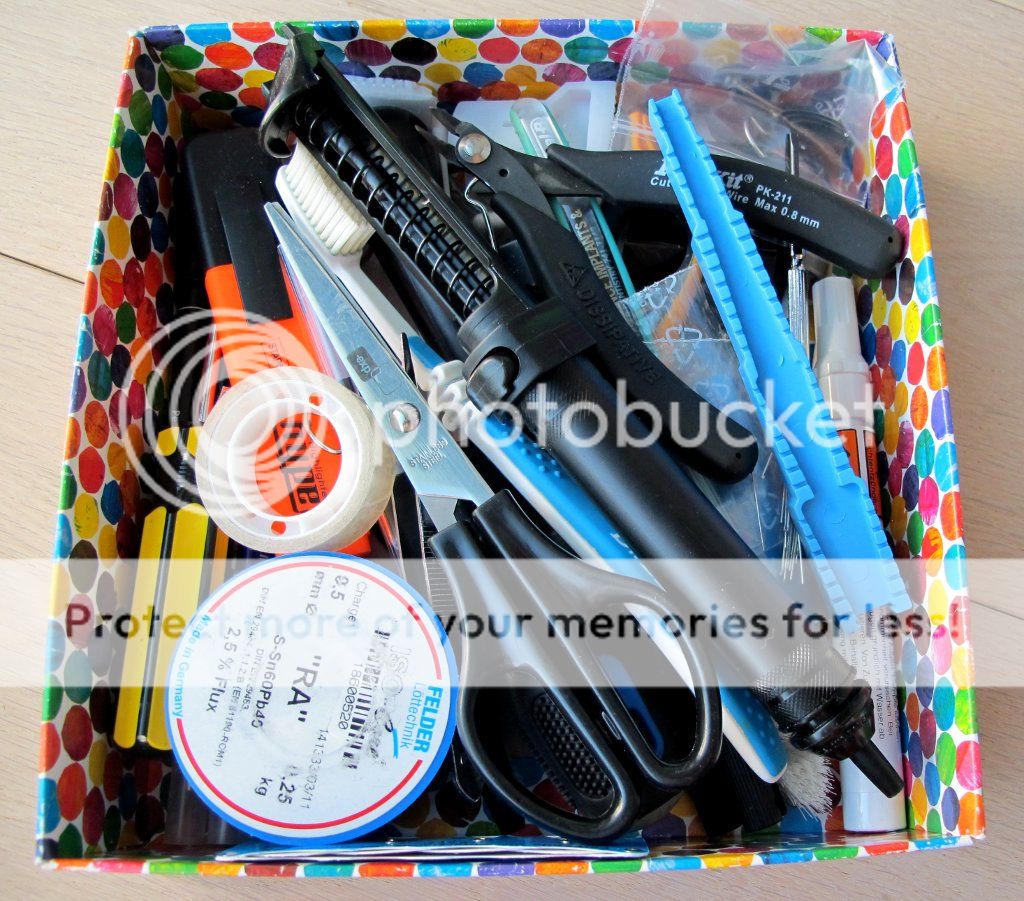
Zum Abisolieren von Kabeln verwende ich ausschließlich folgende Spezialzange, die ich auch immer gerne weiter empfehle. Diese Zange ist nicht billig, aber ich denke sie ist ihr Geld Wert und bringt auch einen gewissen Spaßfaktor beim Arbeiten. Diese Zange entfernt die Isolierung ohne das der Draht dabei beschädigt wird. Man muß nur einmal die Länge einstellen, die man abisolieren möchte und los gehts. Die Zange stellt sich automatisch auf die Kabeldicke und Ummantelungsdicke ein, einfach super.
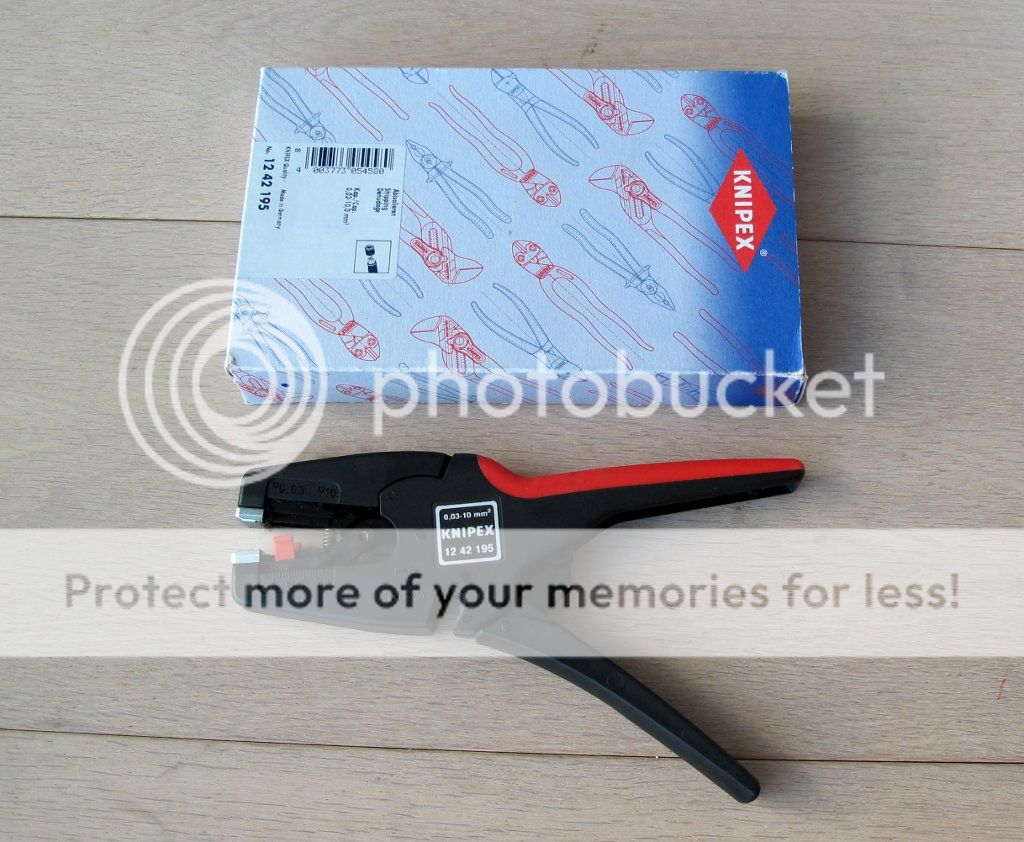
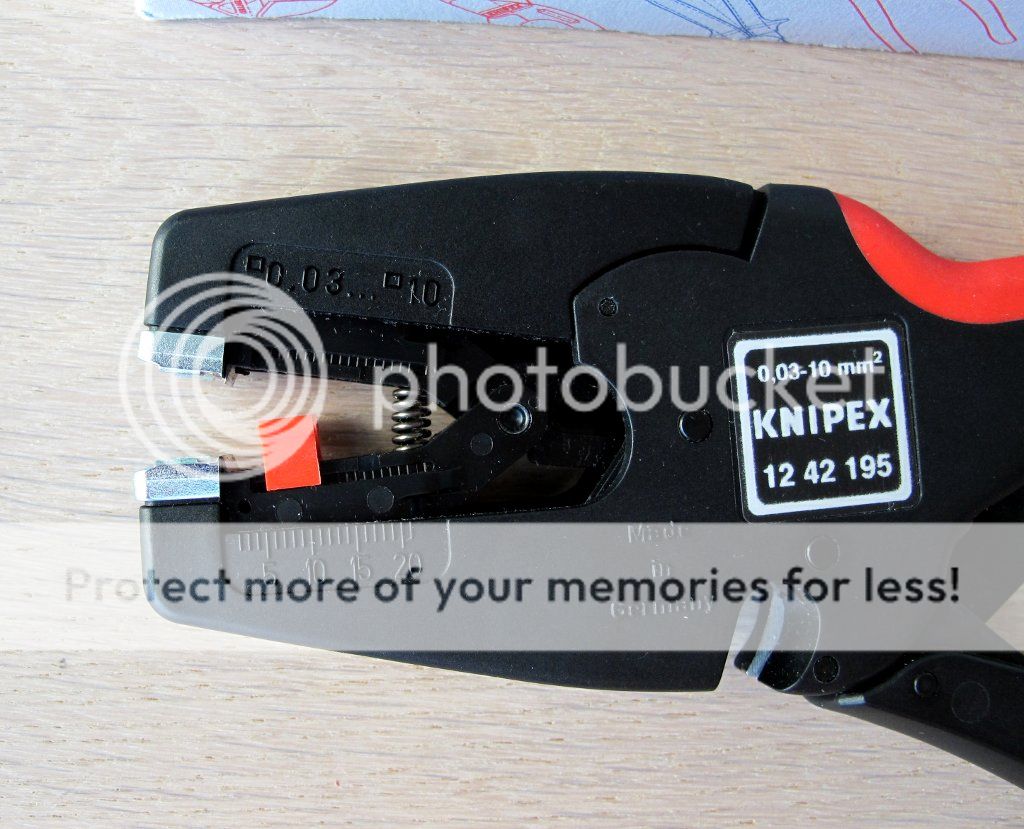
Dann habe ich mir auch eine Spezialzange zum Crimpen von Steckverbindern beschafft, die ist billig und Gold Wert:
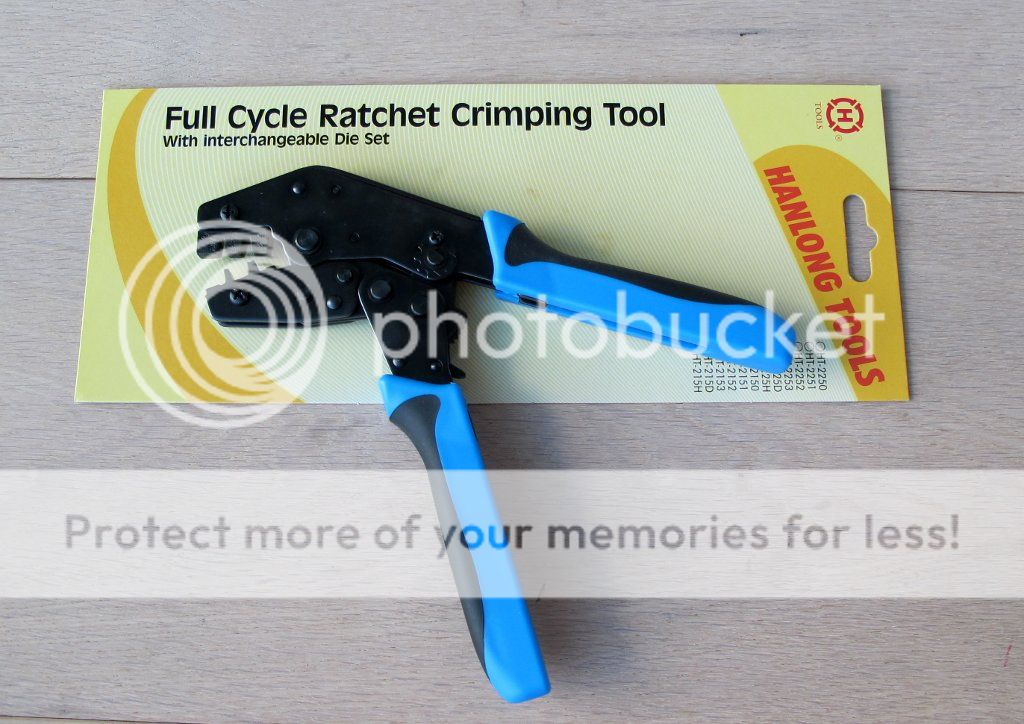
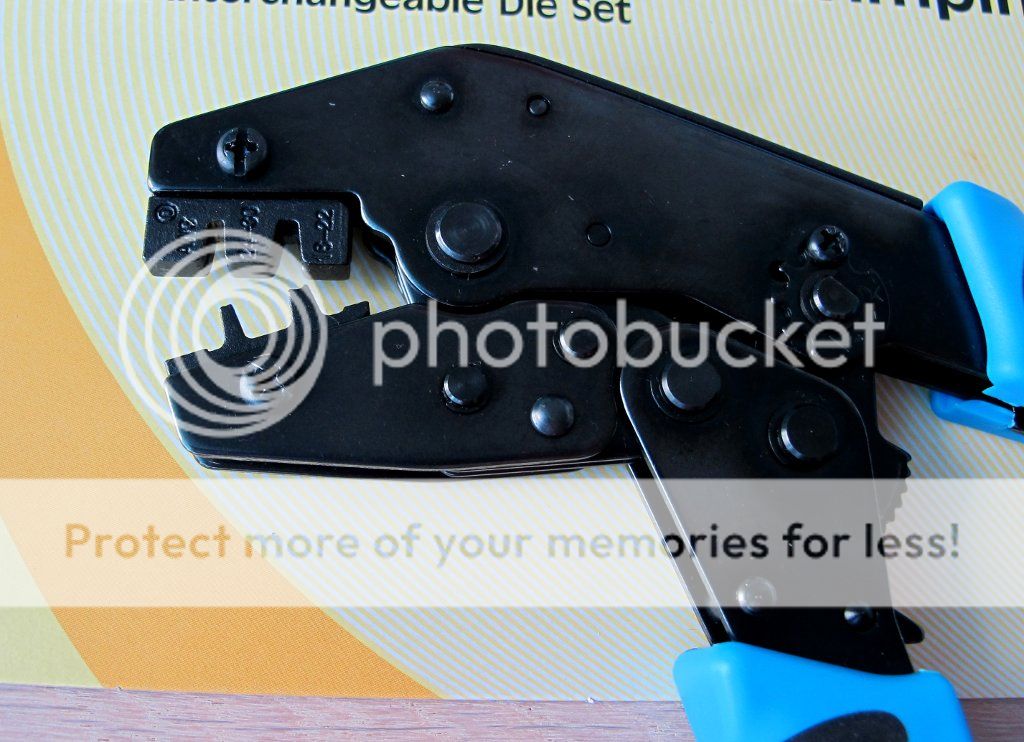
Für Bohrungen und ander mechanische Arbeiten habe ich mir einen Proxxon FBS 240/E gekauft, der ist handlich und leistet sehr gute Dienste:
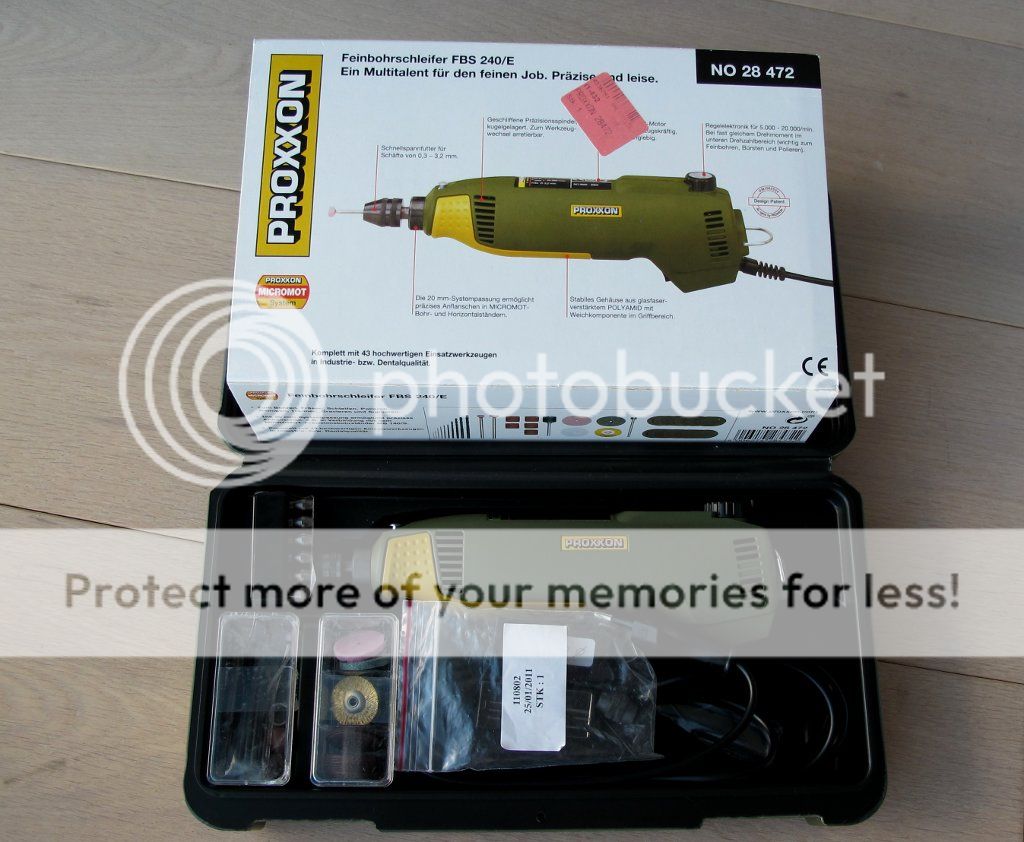
Wenn man mit so einem Tool arbeitet, dann muß man auch eine Brille aufsetzen ! Health & Safety !!
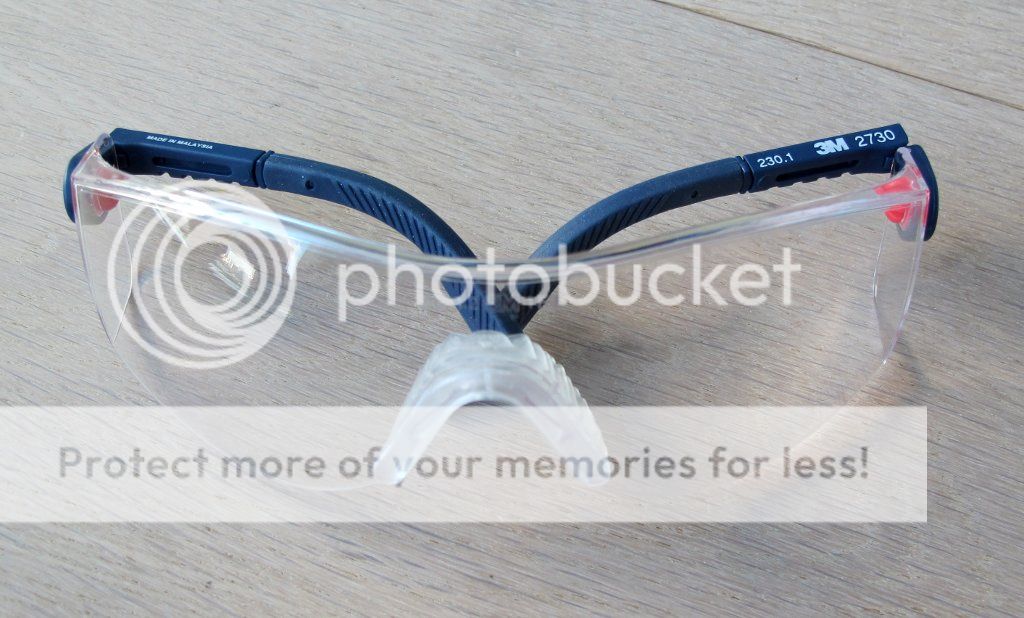
Zum Löten verwende ich den Ersa Tip 260 mit bleistift-förmiger Spitze. Damit konnte ich bisher alle Projekt bearbeiten:
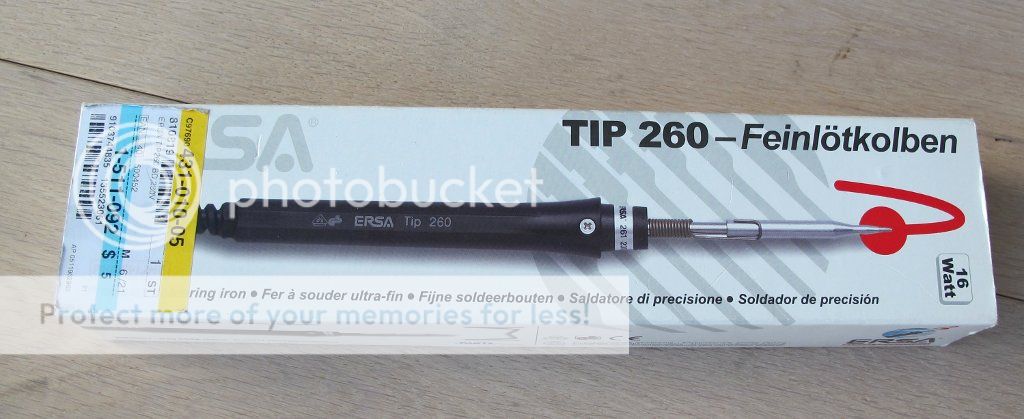
Dazu einen passenden Ständer:
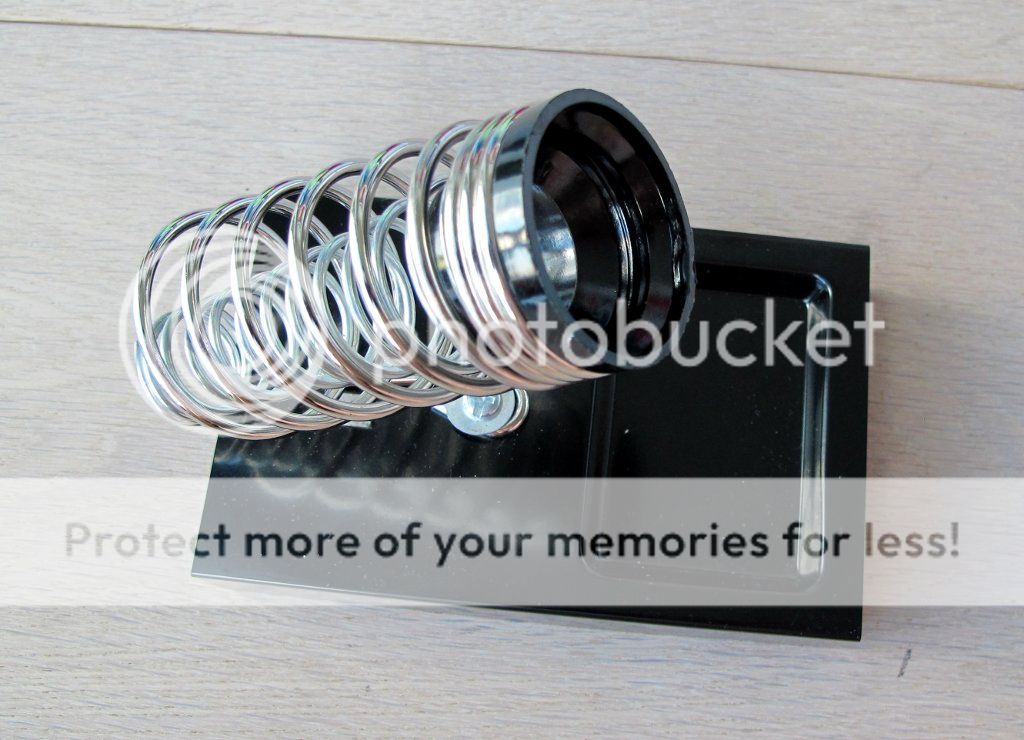
Die Platinen spanne ich meistens in folgenden Platinenhalter ein. Der ist auch Gold Wert.
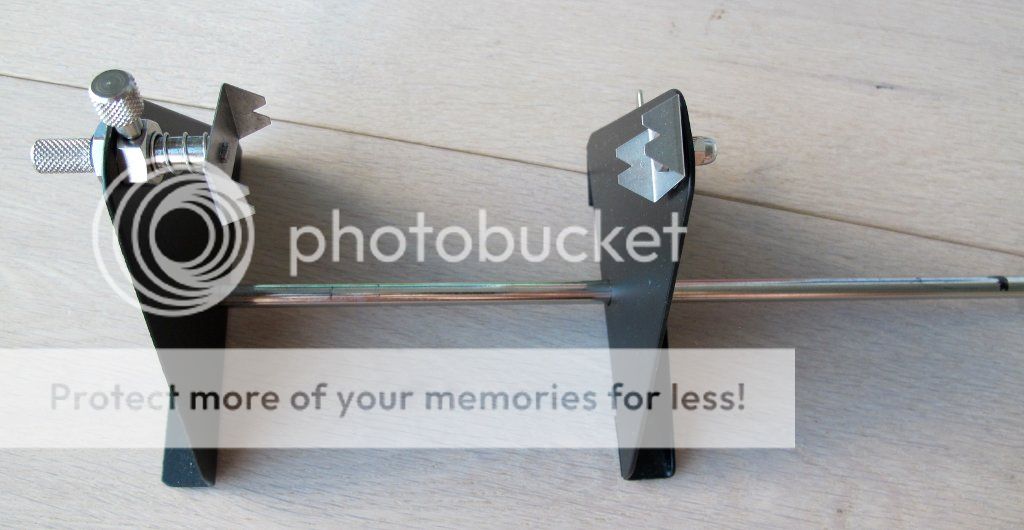
Kleinere Platinen lasse ich mit folgendem Teil halten:
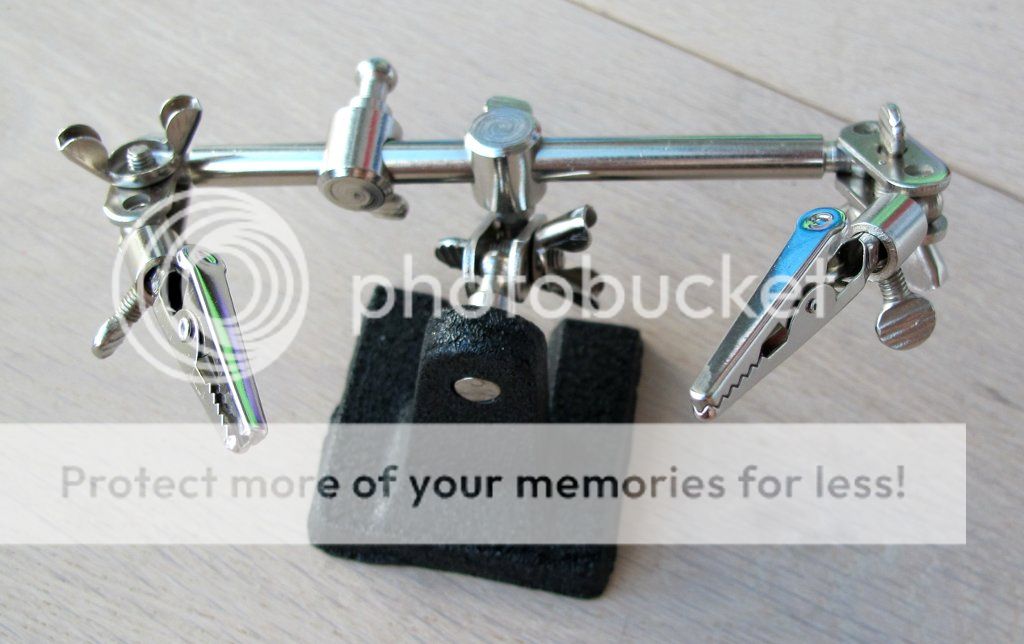
Folgende Zange halte ich für absolut empfehlenswert, denn damit lassen sich auch sehr kleine Bauteile auf der Platine noch gut abschneiden:
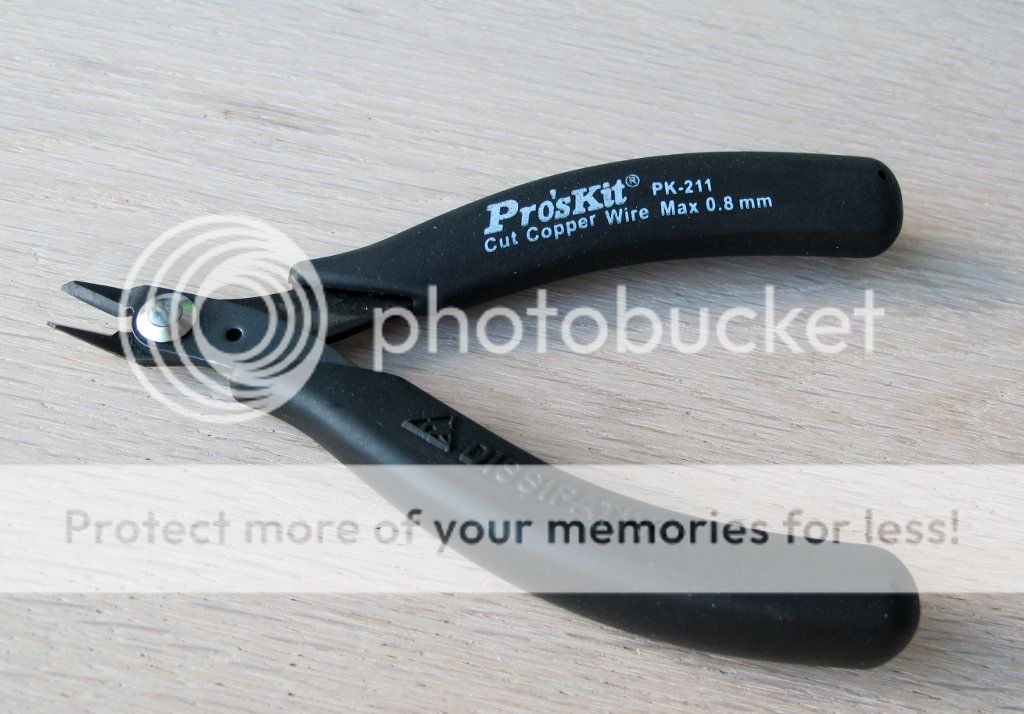
Als nächstes kommt eine Übersicht der Komponenten des Sequenzers. Mann kann ihn ja in unterschiedlichen Ausführungen aufbauen:
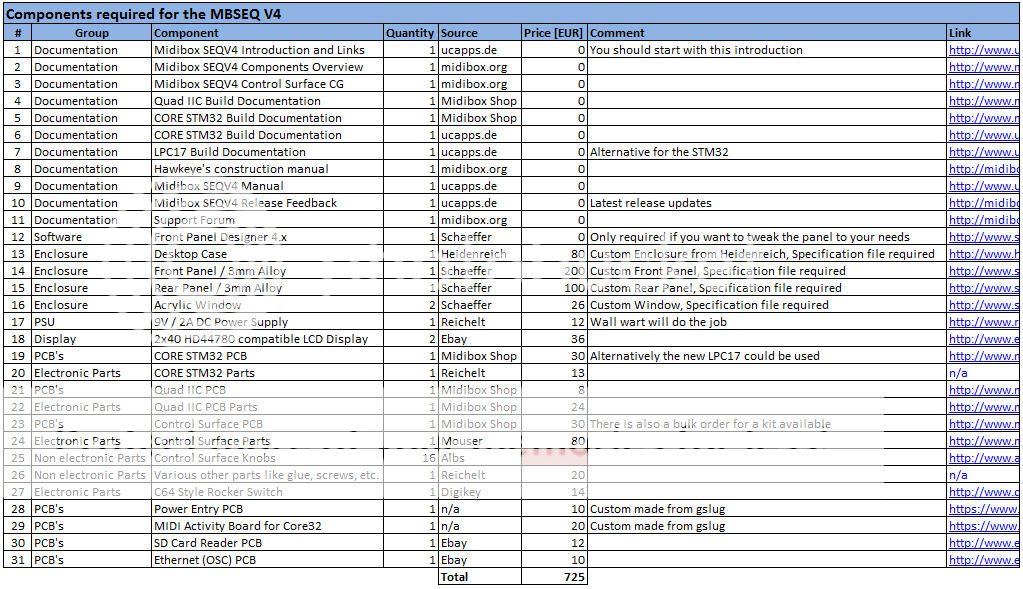
Die wesentlichen Bestandteile meines MBSEQV4 sind also:
- Das Alu Gehäuse von der Firma Heidenreich
- Die Core32 Platine, die die Steuerung und Programmlogik des Sequenzers realisiert. Auf der Platine befindet sich auch der USB Port
- Die Quad IIC Platine, die nochmal 4 MIDI Out Ports, einen DinSync und einen BLM (Button Led Matrix) Port zur Verfügung stellt
- Das Ethernet Modul, welches für das OSC (open sound control) Protokoll benötigt wird. Yes, der Sequenzer hängt mit im Netz !! Hehe, wer kann schon einen Ping auf sein Gear machen

- Das SD Karten Modul zum Lesen und Schreiben der Projektdaten und der Konfigurationsdateien
- Die Bedieneroberfläche mit 16 Encodern und einen Haufen Tastern
- Das Front Panel, welches bei der Firma Schaeffer AG produziert werden kann
- Zwei Displays mit je 2x40 Zeichen
- Steckernetzgerät DC 9V / 2A
Wie man in meiner Kalkulation sieht, ist das Projekt nicht billig, da kommt eine Menge zusammen.