Eine Dokumentation in (vorerst) vier Folgen:
Ende Mai 2021 hatte ich begonnen, meine "Kalimbalimba" getaufte Noisebox zu bauen. Seinen Ursprung hatte das Projekt im Thema "Kontaktmikrofone für Field-Recorder", wo auch der erste Entwurf zu sehen ist :
erster Entwurf
Im Folgenden findet sich nun eine sich auf die wesentlichen Arbeitsschritte beschränkende (
) Dokumentation.
1. Fertigung der Grundplatte:
Hierzu wurde der ursprüngliche Entwurf - aufgeteilt auf zwei Blätter im A4-Format - mittels Teppichklebeband auf eine 10mm Multiplexplatte (Birke) aus der Restekiste geklebt:
(1)Bild 2340
Zur groben Annäherung an die spätere Außenkontur wurden mittels Kappsäge Tangentialschnitte mit ca. 2-3 Millimetern kürzestem Abstand zur Kontur erstellt:
(2)Bild 2341
Die so vorbereitete Grundplatte erhielt auf einer selbstgebastelten Vorrichtung - bestehend aus senkrecht angeordnetem Bandschleifer und Auflagetisch ihre endgültige Form:
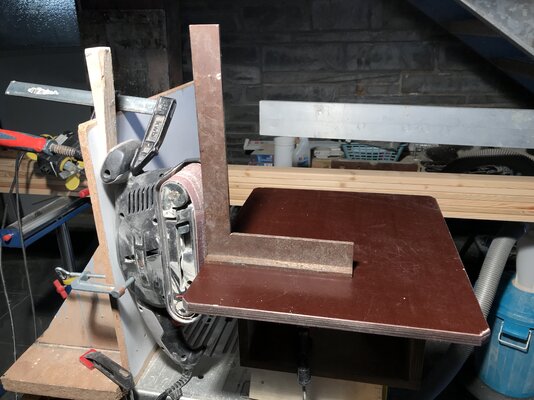
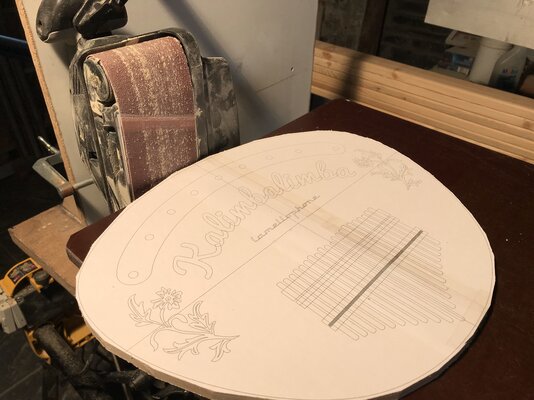
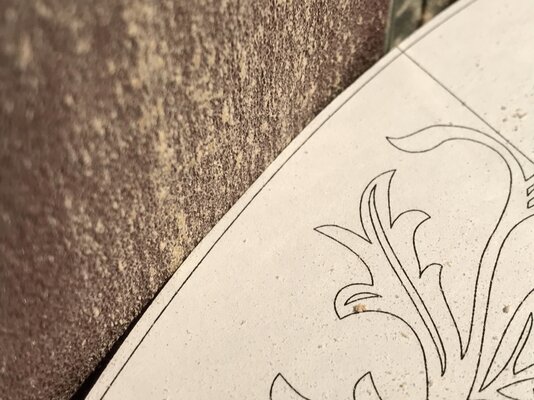
(3-6)Bilder 2343, 2345, 2346, 2347
Die senkrechte Anordnung des Bandschleifers hat dabei zwei Vorteile: zum Einen können wegen des nach unten gerichteten Bandlaufs keine Papierfasern den Blick auf die Konturlinie versperren, zum Anderen erzeugt ein kurzzeitig zu hoher auf das Werkstück ausgeübter Anpressdruck keine horizontalen Kräfte, die ansonsten bei waagerechter Positionierung des Schleifers auftreten könnten.
2. Bau der Zarge:
Da mir eine Zarge aus gebogenem Sperrholz für mein Projekt zu aufwändig erschien und ich zudem bestrebt bin, möglichst alles aus vorhandenem Material zu basteln, entschied ich mich für die Verwertung von Reststücken massiv-stabverleimter Eiche in 20mm Stärke. Die ursprünglich angedachten konstant rechtwinkligen Teilelemente wurden jedoch wieder verworfen, weil sich dadurch eine zu stark variierende Wandstärke der Zarge ergeben hätte. Nach mehreren Planungsversuchen landete ich bei einer symmetrischen Anordnung von miteinander zu verleimenden Teilelementen, die eine maximale Wandstärke und damit eine optimale Verleimbarkeit von Bodenplatte und Decke versprachen:
(7)Bild 3102
Die nach diesem Plan per Kappsäge hergestellten Elemente wurden unter Zuhilfenahme von Paketklebeband jeweils zu Triplets verleimt.
(8)Bild 3107
Diese Vorgehensweise hat den Vorteil, dass die 4 Triplets im getrockneten Zustand sehr verwacklungssicher auf der Grundplatte positionierbar sind, sodass am folgenden Tag die Verleimung mit der Innenseite der Grundplatte stattfinden konnte:
(9)Bild 3112
Die Abtragung des Überstandes wurde wieder mit der bereits beschriebenen Anordnung des Bandschleifers vorgenommen. Da es sich hierbei um hartes Eichenholz handelte und einiges an Material abgetragen werden musste, ging ich dabei schrittweise beginnend mit grober 40er über 80er zu 120er Körnung vor.
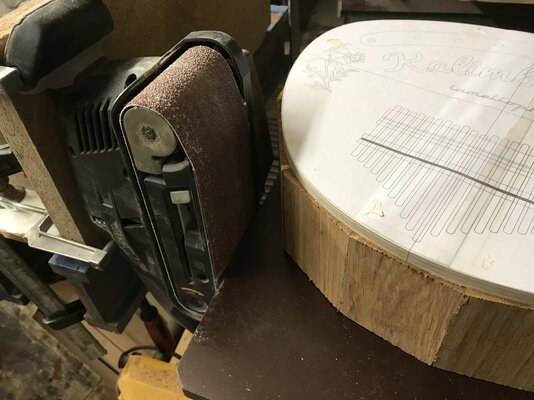
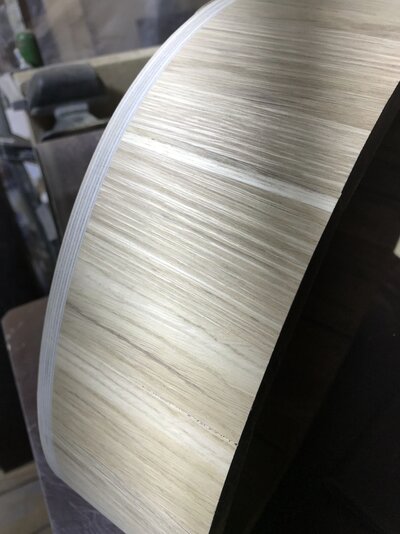
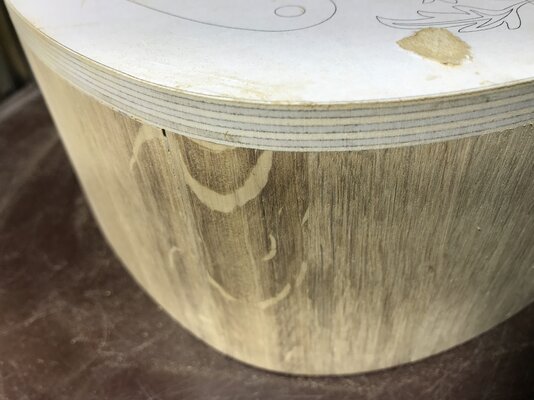
(10-13)Bild 3114, 3121, 3122, 3123
3. Die Decke:
Ursprünglich angedacht war die Verwertung eines Paulownia-Reststücks, welches mir aber wegen des zwischenzeitlichen Fundes uralter Nadelholzregalbretter als zu schade erschien. Die 60 Jahre alten, 18mm dicken Bretter mussten aber wegen Lagerung im Heuschober erstmal mittels Bürste und Spachtel vom anhaftenden Staub und Mausekot befreit werden, bevor sie in meinem METABO-Abrichthobel auf die gewünschte Dicke von 7,5 Millimetern gebracht werden konnten. Als Nebenprodukt entstand ein riesiger Sack mit Hobelspänen, die wir vortrefflich im Gemüsegarten zum Mulchen verwenden werden...
Drei dieser abgerichteten Teilstücke wurden sodann miteinander zur Decke verleimt:
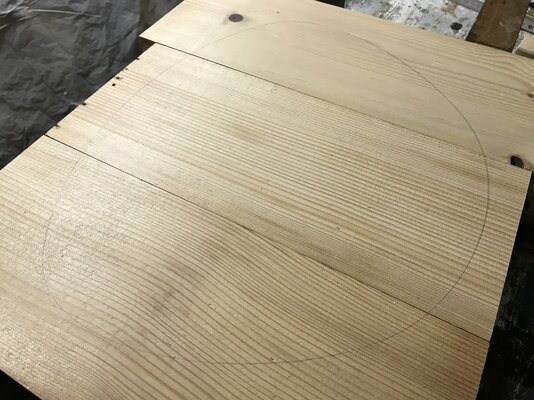
(14-15)Bild 3073, 3071
Nach dem groben Zuschnitt mit der Stichsäge konnte die Verleimung mit der Zarge stattfinden:
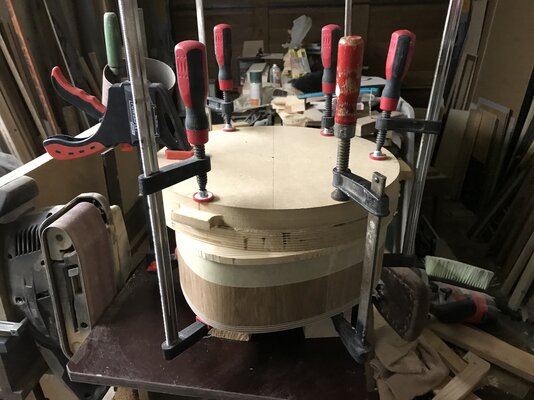
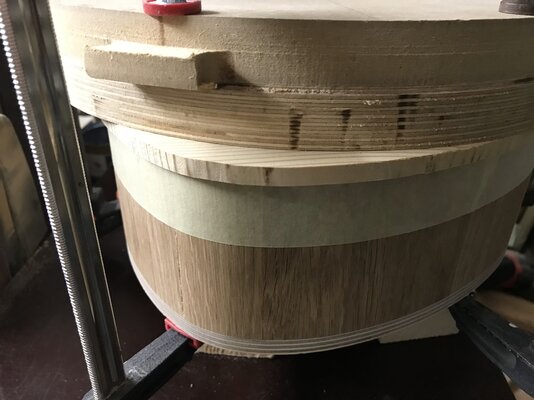
(16-17)Bild 3124, 3125
Um zu verhindern, dass austretender Leim auf die Zarge rinnt, wurde ein Streifen Malerkrepp verwendet. Leimflecken beeinträchtigen nämlich nachfolgende Oberflächenbehandlungen, weil die Eindringtiefe von Lasuren, Beizen, Lacken oder Ölen damit verringert wird. Also besser Vorbohren als Nachbeugen (oderso...).
Nach dem Bündigschleifen (Bündigfräsen erschien mir wegen möglicher Ausrisse an Stellen ungünstigen Maserungsverlaufs zu gefährlich) sah der rohe Korpus dann so aus:
(18)Bild 3137
4. Montageöffnung und Resonanzloch:
Da der Korpus nun eine hermetisch geschlossene "Kiste" darstellte, musste an der Unterseite eine Öffnung zur Montage der zur Tonerzeugung und -abnahme erforderlichen Hardware geschaffen werden. Lange habe ich mit mir gehadert und wollte ursprünglich eine Öffnung einfräsen, die eine exakte, aber verkleinerte Kopie der Außenkontur dargestellt hätte. Ebenfalls der einzupassende Deckel hätte dann diese komplexe Form haben und mindestens zwei Frässchablonen hätten erstellt werden müssen. Das erschien mir dann doch zu aufwändig. Also wurde der Fräszirkel gezückt und das Ganze relativ zügig realisiert:
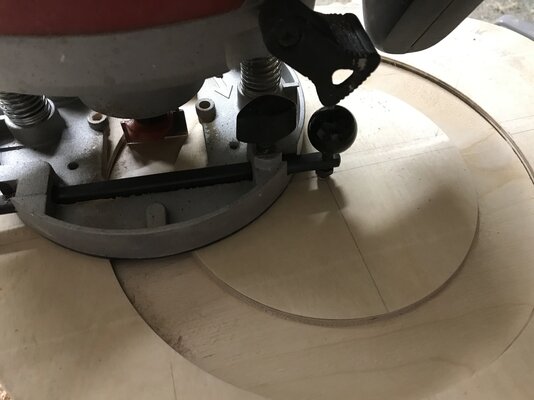
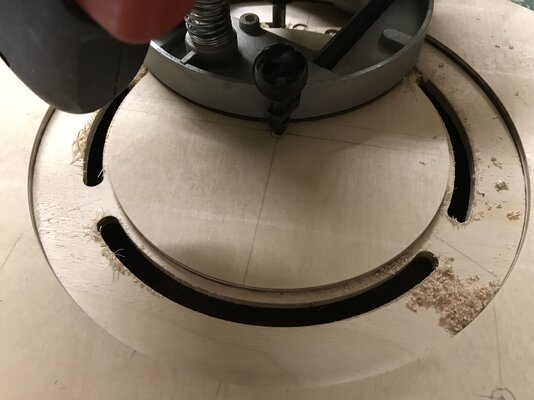
(19-20)Bild 3212, 3213
Die drei dünnen Stege lässt man stehen, weil ansonsten die Zentrierung der Fräse nicht mehr gegeben wäre und der Fräskopf dann quasi führungslos die angestrebte Kreisform der Öffnung versaubeuteln würde. Die Stege wurden natürlich anschließend durchtrennt und sauber weggeschliffen.
Fortsetzung folgt...
Ende Mai 2021 hatte ich begonnen, meine "Kalimbalimba" getaufte Noisebox zu bauen. Seinen Ursprung hatte das Projekt im Thema "Kontaktmikrofone für Field-Recorder", wo auch der erste Entwurf zu sehen ist :
erster Entwurf
Im Folgenden findet sich nun eine sich auf die wesentlichen Arbeitsschritte beschränkende (

1. Fertigung der Grundplatte:
Hierzu wurde der ursprüngliche Entwurf - aufgeteilt auf zwei Blätter im A4-Format - mittels Teppichklebeband auf eine 10mm Multiplexplatte (Birke) aus der Restekiste geklebt:
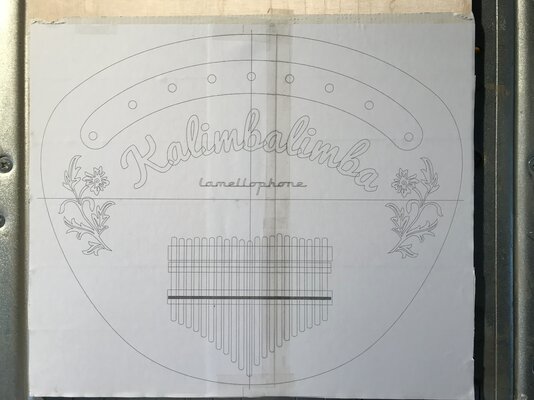
Zur groben Annäherung an die spätere Außenkontur wurden mittels Kappsäge Tangentialschnitte mit ca. 2-3 Millimetern kürzestem Abstand zur Kontur erstellt:
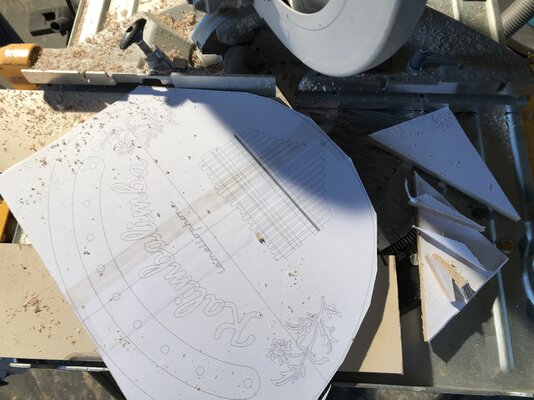
Die so vorbereitete Grundplatte erhielt auf einer selbstgebastelten Vorrichtung - bestehend aus senkrecht angeordnetem Bandschleifer und Auflagetisch ihre endgültige Form:
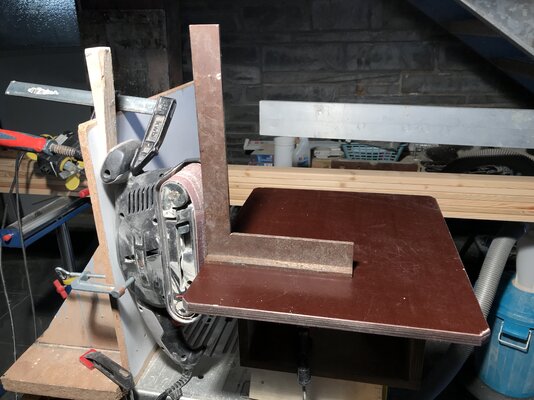
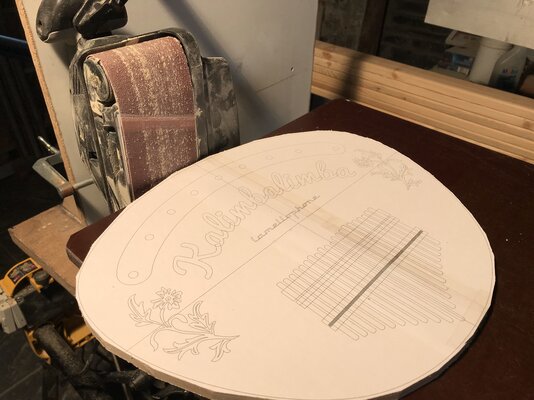
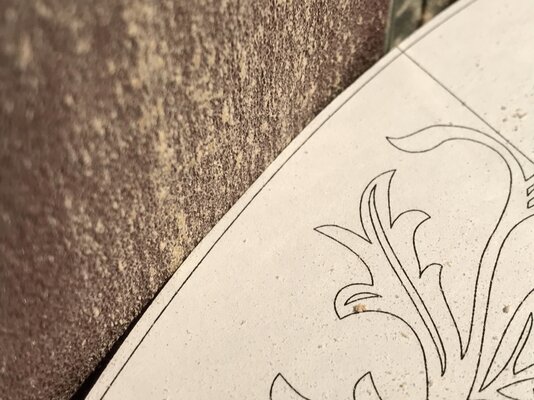
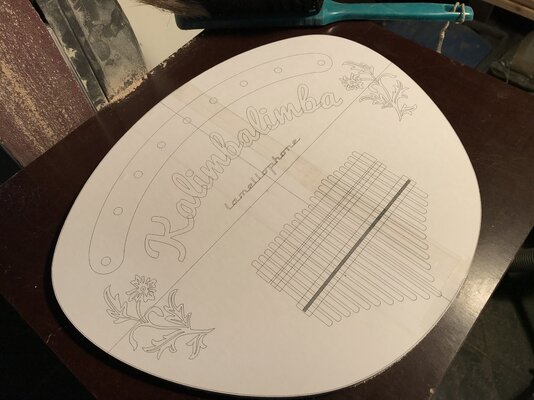
Die senkrechte Anordnung des Bandschleifers hat dabei zwei Vorteile: zum Einen können wegen des nach unten gerichteten Bandlaufs keine Papierfasern den Blick auf die Konturlinie versperren, zum Anderen erzeugt ein kurzzeitig zu hoher auf das Werkstück ausgeübter Anpressdruck keine horizontalen Kräfte, die ansonsten bei waagerechter Positionierung des Schleifers auftreten könnten.
2. Bau der Zarge:
Da mir eine Zarge aus gebogenem Sperrholz für mein Projekt zu aufwändig erschien und ich zudem bestrebt bin, möglichst alles aus vorhandenem Material zu basteln, entschied ich mich für die Verwertung von Reststücken massiv-stabverleimter Eiche in 20mm Stärke. Die ursprünglich angedachten konstant rechtwinkligen Teilelemente wurden jedoch wieder verworfen, weil sich dadurch eine zu stark variierende Wandstärke der Zarge ergeben hätte. Nach mehreren Planungsversuchen landete ich bei einer symmetrischen Anordnung von miteinander zu verleimenden Teilelementen, die eine maximale Wandstärke und damit eine optimale Verleimbarkeit von Bodenplatte und Decke versprachen:

Die nach diesem Plan per Kappsäge hergestellten Elemente wurden unter Zuhilfenahme von Paketklebeband jeweils zu Triplets verleimt.
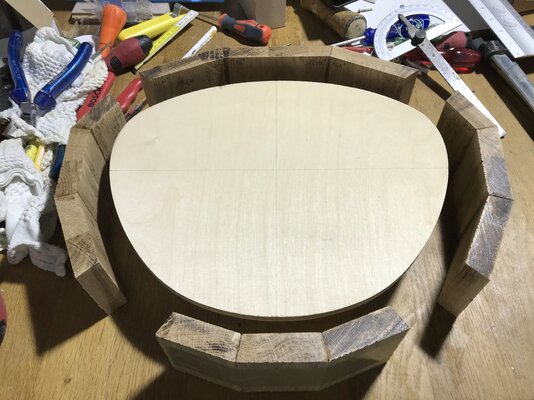
Diese Vorgehensweise hat den Vorteil, dass die 4 Triplets im getrockneten Zustand sehr verwacklungssicher auf der Grundplatte positionierbar sind, sodass am folgenden Tag die Verleimung mit der Innenseite der Grundplatte stattfinden konnte:
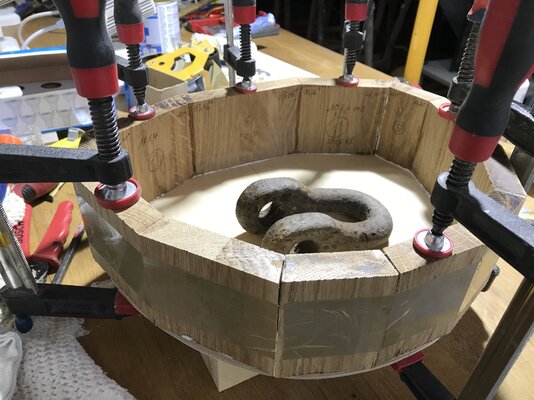
Die Abtragung des Überstandes wurde wieder mit der bereits beschriebenen Anordnung des Bandschleifers vorgenommen. Da es sich hierbei um hartes Eichenholz handelte und einiges an Material abgetragen werden musste, ging ich dabei schrittweise beginnend mit grober 40er über 80er zu 120er Körnung vor.
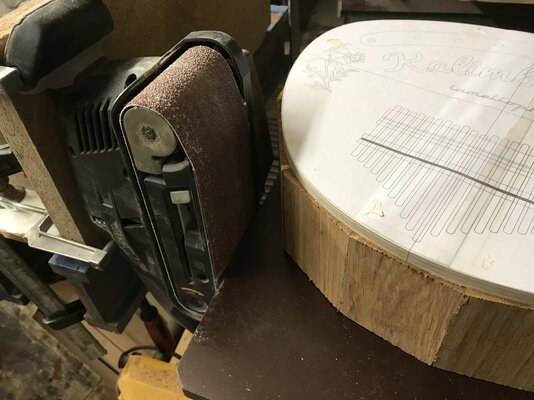
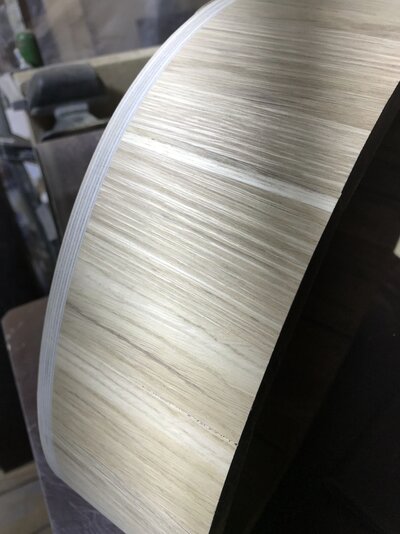
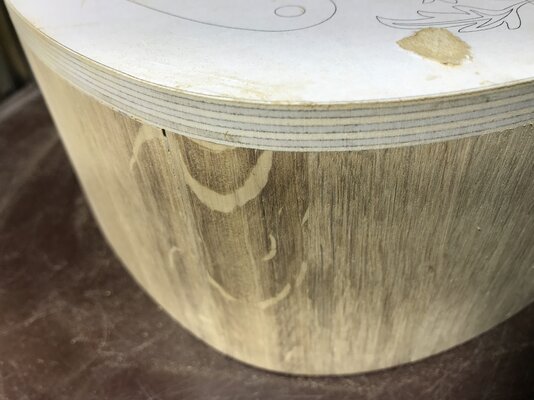
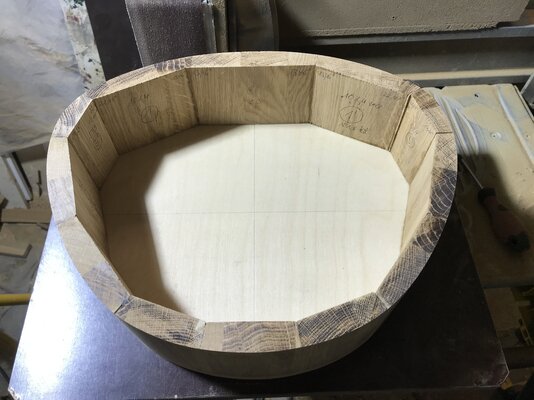
3. Die Decke:
Ursprünglich angedacht war die Verwertung eines Paulownia-Reststücks, welches mir aber wegen des zwischenzeitlichen Fundes uralter Nadelholzregalbretter als zu schade erschien. Die 60 Jahre alten, 18mm dicken Bretter mussten aber wegen Lagerung im Heuschober erstmal mittels Bürste und Spachtel vom anhaftenden Staub und Mausekot befreit werden, bevor sie in meinem METABO-Abrichthobel auf die gewünschte Dicke von 7,5 Millimetern gebracht werden konnten. Als Nebenprodukt entstand ein riesiger Sack mit Hobelspänen, die wir vortrefflich im Gemüsegarten zum Mulchen verwenden werden...
Drei dieser abgerichteten Teilstücke wurden sodann miteinander zur Decke verleimt:
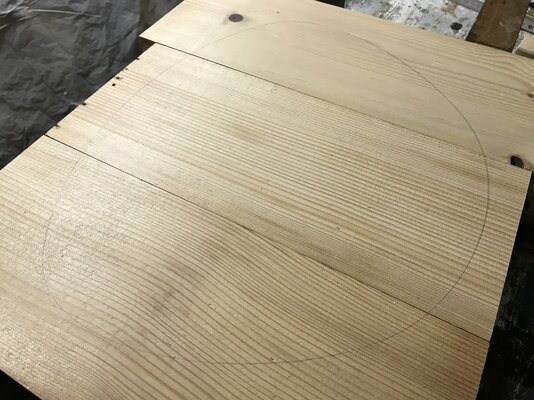
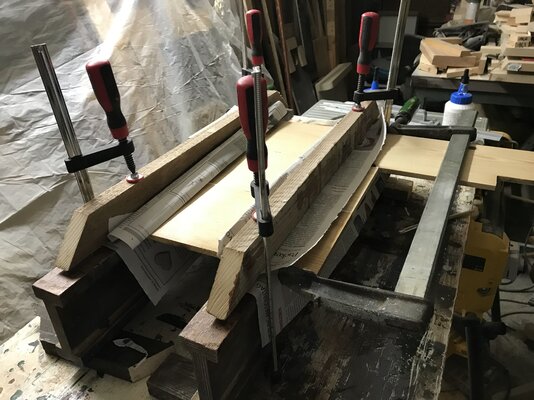
Nach dem groben Zuschnitt mit der Stichsäge konnte die Verleimung mit der Zarge stattfinden:
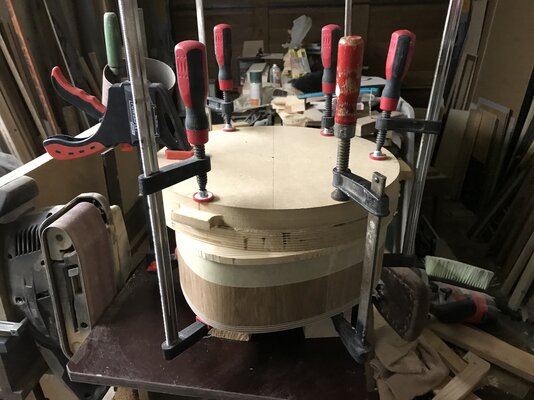
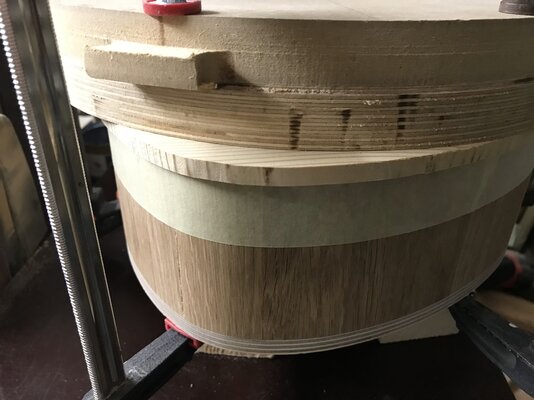
(16-17)Bild 3124, 3125
Um zu verhindern, dass austretender Leim auf die Zarge rinnt, wurde ein Streifen Malerkrepp verwendet. Leimflecken beeinträchtigen nämlich nachfolgende Oberflächenbehandlungen, weil die Eindringtiefe von Lasuren, Beizen, Lacken oder Ölen damit verringert wird. Also besser Vorbohren als Nachbeugen (oderso...).
Nach dem Bündigschleifen (Bündigfräsen erschien mir wegen möglicher Ausrisse an Stellen ungünstigen Maserungsverlaufs zu gefährlich) sah der rohe Korpus dann so aus:
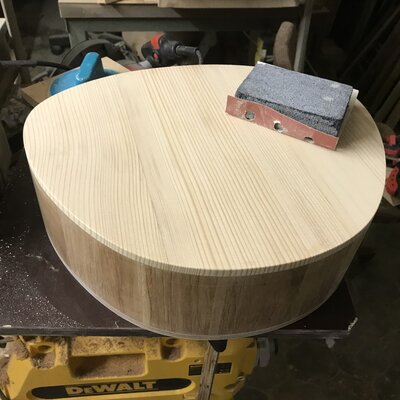
4. Montageöffnung und Resonanzloch:
Da der Korpus nun eine hermetisch geschlossene "Kiste" darstellte, musste an der Unterseite eine Öffnung zur Montage der zur Tonerzeugung und -abnahme erforderlichen Hardware geschaffen werden. Lange habe ich mit mir gehadert und wollte ursprünglich eine Öffnung einfräsen, die eine exakte, aber verkleinerte Kopie der Außenkontur dargestellt hätte. Ebenfalls der einzupassende Deckel hätte dann diese komplexe Form haben und mindestens zwei Frässchablonen hätten erstellt werden müssen. Das erschien mir dann doch zu aufwändig. Also wurde der Fräszirkel gezückt und das Ganze relativ zügig realisiert:
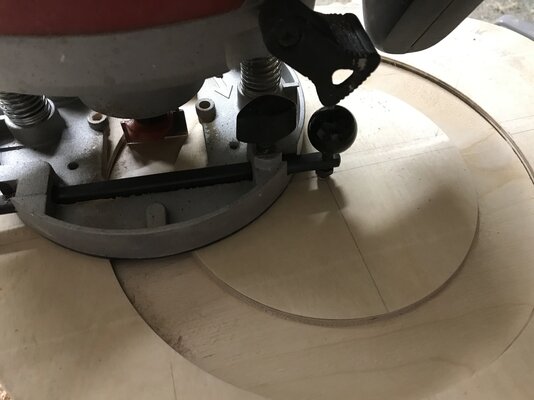
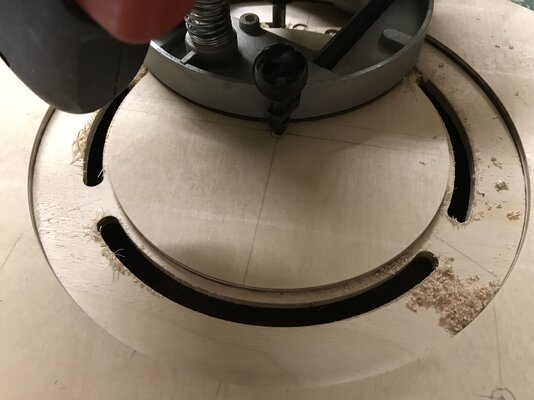
(19-20)Bild 3212, 3213
Die drei dünnen Stege lässt man stehen, weil ansonsten die Zentrierung der Fräse nicht mehr gegeben wäre und der Fräskopf dann quasi führungslos die angestrebte Kreisform der Öffnung versaubeuteln würde. Die Stege wurden natürlich anschließend durchtrennt und sauber weggeschliffen.
Fortsetzung folgt...
Zuletzt bearbeitet: